In the world of measurements and calibrations, precision is paramount. Industries spanning manufacturing, healthcare, and technology rely heavily on accurate measurements to ensure the quality and reliability of their processes and products. This is where the National Accreditation Board for Testing and Calibration Laboratories (NABL) steps in, setting the gold standard for laboratory accreditation. Choosing a NABL accredited laboratory for calibration needs brings a host of advantages that go beyond mere compliance.
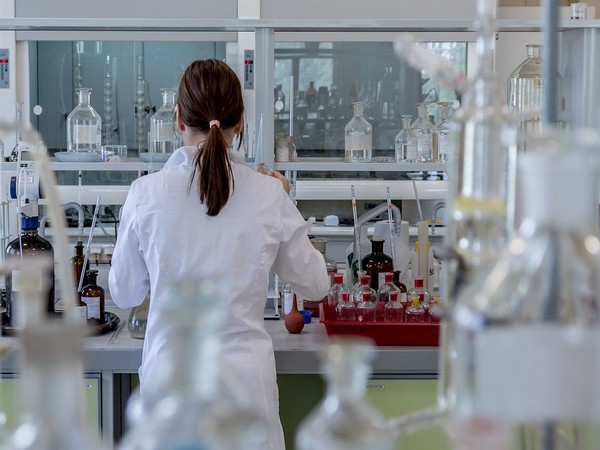
Stringent Quality Standards:
NABL accreditation is a mark of compliance with rigorous quality standards. Laboratories undergo a thorough evaluation process, ensuring that they meet the highest benchmarks in terms of competence and technical proficiency. This commitment to excellence translates into precise and reliable calibration services.
Enhanced Accuracy:
Accuracy is the cornerstone of any calibration process. NABL-accredited laboratories utilize advanced equipment and follow stringent procedures to guarantee the highest level of accuracy in their measurements. Businesses can trust that their instruments and equipment will be calibrated with the utmost precision, contributing to improved operational efficiency.
Compliance with Industry Regulations:
Industries are subject to a myriad of regulations and standards to ensure the safety and quality of their products. Choosing a NABL accredited laboratory for calibration ensures alignment with these industry-specific regulations. This not only safeguards against potential legal issues but also establishes a foundation for consistent quality assurance.
Global Recognition:
NABL accreditation is globally recognized, signifying that the laboratory has met international standards for testing and calibration. This recognition is particularly crucial for businesses engaged in international trade or collaborations, as it instills confidence in partners and customers regarding the reliability of the calibration services.
Continuous Improvement Culture:
NABL accreditation is not a one-time achievement but an ongoing commitment to quality. Accredited laboratories follow a culture of continuous improvement, regularly updating their processes and technologies to stay at the forefront of advancements in their respective fields. This dedication ensures that clients receive calibration services that evolve with the industry’s best practices.
Traceability and Documentation:
NABL-accredited laboratories prioritize traceability, providing a clear and documented path of the calibration process. This traceability ensures that the measurements are verifiable and can be traced back to national or international standards. Transparent documentation also aids in audits, providing a comprehensive record of the calibration history.
Customer Confidence:
Choosing a NABL accredited laboratory instills confidence in customers and partners. It signifies a commitment to quality, reliability, and precision. Businesses can use NABL accreditation as a marketing advantage, demonstrating to clients that their processes and products are backed by precise and credible calibration services.
Reduced Downtime and Costs:
Accurate and reliable measurements contribute to increased operational efficiency. Equipment that is precisely calibrated is less likely to malfunction or cause errors, reducing downtime and the associated costs. This proactive approach to calibration can lead to long-term savings by preventing costly disruptions in production or services.
Conclusion
In the realm of precision, NABL accreditation stands as a beacon of excellence. Choosing a NABL accredited laboratory for calibration needs offers a myriad of advantages, ranging from stringent quality standards and enhanced accuracy to global recognition and customer confidence. As industries continue to evolve, the importance of precise measurements becomes increasingly evident. Embrace the advantages of NABL accreditation and elevate your calibration experience to new heights of reliability and excellence.
Frequently Asked Questions:
How often should industries consider calibrating their instruments and equipment?
The frequency of calibration depends on various factors, including the type of instrument, its usage, and industry regulations. In general, industries should establish a regular calibration schedule based on the criticality of the measurements. For high-precision instruments or those used in critical processes, annual calibration may be necessary. However, less critical instruments may require calibration every 2-3 years. Regular calibration ensures accuracy, reliability, and compliance with industry standards.
How frequently do NABL-accredited laboratories undergo evaluations to maintain accreditation?
NABL-accredited laboratories undergo evaluations regularly to maintain accreditation. The specific frequency varies, but it typically involves a surveillance audit at least once a year. Additionally, laboratories may undergo a re-assessment every few years. These evaluations ensure that the laboratory continues to meet NABL stringent standards for competence, technical proficiency, and adherence to quality management systems. The frequency of evaluations underscores the commitment to maintaining the highest standards in testing and calibration services.
How often do advancements in calibration technologies impact the services provided by NABL-accredited labs?
Advancements in calibration technologies can impact NABL-accredited labs frequently. Accredited laboratories are committed to staying abreast of technological advancements to enhance the precision and efficiency of their services. The frequency of these impacts depends on the rate of technological innovation in the calibration field. Accredited labs often invest in state-of-the-art equipment and regularly update their methodologies to incorporate the latest advancements, ensuring that clients benefit from the most accurate and up-to-date calibration services.
How regularly should businesses update their calibration procedures to align with industry best practices?
Businesses should update their calibration procedures regularly to align with industry best practices. This frequency depends on factors such as changes in industry standards, advancements in calibration technologies, or modifications to the instruments being calibrated. A best practice is to review and update calibration procedures at least annually or whenever there is a significant change in equipment or regulations.
Author Bio
Mr. Parthiv Kinariwala is a leading expert in calibration and testing services, with over 20 years of experience in the industry. As the founder of Prism Calibration, established in 2004, Mr. Kinariwala has been at the forefront of delivering precise and reliable calibration, testing, and validation solutions across various industries. His expertise in providing services that meet international calibration standards has earned the trust of major clients, including Reliance Industries, Zydus Cadila, Indian Oil, ONGC, Adani, and Tata.
With a deep understanding of instrumentation, measurement accuracy, and industrial testing, Mr. Kinariwala ensures that each client receives exceptional service tailored to their specific needs. His unwavering commitment to quality and precision has established Prism Calibration as a trusted partner for some of the largest and most respected organizations in the industry.