Rotameters are indispensable tools in various industries for measuring the flow rate of fluids. However, like any measuring instrument, they require proper calibration to ensure accurate readings. Despite their reliability, common issues can arise during calibration, leading to inaccurate measurements. This article explores the most common issues encountered during rotameter calibration and provides valuable troubleshooting tips to address them effectively.
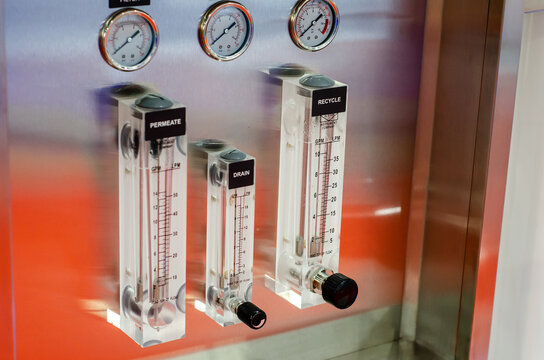
Introduction to Rotameters
Rotameters, also known as variable area flow meters, operate based on the principle of fluid flowing through a conically shaped tube, causing a float to rise or fall, indicating the flow rate. Calibration is crucial to maintain the accuracy of these instruments, ensuring precise measurements across different operating conditions.
Common Issues in Rotameter Calibration
Inaccurate Readings:
One of the most prevalent issues in rotameter calibration is inaccurate readings. This can occur due to factors such as improper installation, fluid properties, or mechanical damage to the instrument. Inaccurate readings can lead to incorrect process control decisions, resulting in inefficiencies or product quality issues.
Drifting Readings:
Drifting readings occur when the flow rate indication fluctuates over time, even under stable operating conditions. This phenomenon can be caused by changes in fluid properties, temperature, or pressure variations within the system. Drifting readings can be particularly challenging to troubleshoot as they may indicate underlying issues that require thorough investigation.
Mechanical Damage:
Mechanical damage to the rotameter can significantly affect its calibration and performance. Damage to the float, tube, or other components can disrupt the flow of fluid, leading to inaccurate readings. Regular inspection and maintenance are essential to identify and address mechanical damage promptly.
Troubleshooting Tips
To effectively troubleshoot common issues in rotameter calibration, consider the following tips:
Check for Blockages:
Inspect the rotameter for any blockages or obstructions in the flow path. Clearing any debris or buildup can help restore accurate readings and prevent further issues.
Ensure Proper Installation:
Verify that the rotameter is installed correctly according to manufacturer guidelines. Improper installation can lead to misalignment or leaks, affecting calibration and performance.
Verify Fluid Properties:
Ensure that the fluid properties, such as viscosity and density, match the calibration parameters specified for the rotameter. Variations in fluid properties can impact the accuracy of measurements.
Inspect for Mechanical Damage:
Regularly inspect the rotameter for signs of mechanical damage, such as cracks, dents, or corrosion. Address any issues promptly to prevent further deterioration of performance.
Calibration Techniques
Several calibration techniques can be employed to ensure the accuracy of rotameters:
Gravity Method:
The gravity method involves calibrating the rotameter using a known volume of fluid under the influence of gravity. This method is simple and cost-effective, suitable for basic calibration requirements.
Ball Float Method:
The ball float method utilizes a calibrated float that rises or falls within the rotameter tube, indicating the flow rate. This method offers higher accuracy and is suitable for precise calibration needs.
Displacement Method:
The displacement method involves measuring the displacement of fluid by the float as it moves through the rotameter tube. This method is highly accurate and commonly used in laboratory settings.
Regular Maintenance Practices
To ensure reliable performance and accurate calibration, implement the following maintenance practices:
Cleaning Procedures:
Regularly clean the rotameter components to remove any buildup or contaminants that may affect performance. Use appropriate cleaning agents and procedures recommended by the manufacturer.
Lubrication:
Apply lubrication to moving parts of the rotameter to reduce friction and ensure smooth operation. Use lubricants compatible with the materials of construction to prevent damage or degradation.
Inspection Schedule:
Establish a routine inspection schedule to detect any signs of wear, damage, or calibration drift. Regular inspections allow for timely maintenance and calibration adjustments to maintain optimal performance.
Advanced Calibration Methods
Advanced calibration methods leverage technology to enhance the accuracy and efficiency of rotameter calibration:
Electronic Calibration:
Electronic calibration systems utilize sensors and digital interfaces to monitor and adjust flow rate measurements automatically. These systems offer real-time calibration feedback and can be integrated into automated process control systems.
Computerized Calibration Systems:
Computerized calibration systems employ software algorithms to analyze calibration data and optimize flow rate measurements. These systems offer advanced data processing capabilities and can streamline calibration procedures for complex applications.
Case Studies:
Explore real-life examples of calibration issues encountered in various industries and the solutions implemented to address them effectively.
Best Practices for Rotameter Calibration
Adopt the following best practices to ensure successful rotameter calibration:
Documentation:
Maintain detailed records of calibration procedures, including dates, parameters, and results. Documentation provides a historical reference for tracking calibration performance and identifying trends over time.
Training Programs:
Implement training programs for personnel involved in rotameter calibration and maintenance. Proper training ensures that staff members are proficient in calibration procedures and equipped to troubleshoot common issues effectively.
Future Trends in Rotameter Technology
As technology continues to evolve, future trends in rotameter technology may include:
Advancements in Calibration Techniques:
Innovations in calibration techniques may lead to increased accuracy and efficiency in rotameter calibration processes. Integration of advanced sensors and algorithms can enhance calibration precision and reliability.
Automation:
Automation of rotameter calibration processes through the use of robotics and artificial intelligence can streamline calibration procedures and reduce human error. Automated calibration systems offer potential cost savings and increased productivity.
Conclusion
Effective calibration is essential for maintaining the accuracy and reliability of rotameters in various industrial applications. By understanding common calibration issues and implementing troubleshooting tips and best practices, users can ensure optimal performance and minimize measurement errors.
FAQs (Frequently Asked Questions)
Why is calibration important for rotameters?
Calibration ensures that rotameters provide accurate flow rate measurements, essential for process control and quality assurance.
What are some signs that indicate a need for rotameter calibration?
Signs such as drifting readings, inconsistent measurements, or mechanical damage may indicate a need for calibration.
How often should rotameters be calibrated?
The frequency of calibration depends on factors such as application requirements, operating conditions, and manufacturer recommendations. Generally, rotameters should be calibrated regularly to maintain accuracy.
Can I calibrate rotameters myself, or should I seek professional assistance?
While basic calibration procedures can be performed by trained personnel, complex calibration tasks or issues may require professional assistance from experienced technicians or calibration laboratories.
What are the consequences of using uncalibrated rotameters?
Using uncalibrated rotameters can lead to inaccurate flow rate measurements, compromising process efficiency, product quality, and safety.
Author Bio
Mr. Parthiv Kinariwala is a leading expert in calibration and testing services, with over 20 years of experience in the industry. As the founder of Prism Calibration, established in 2004, Mr. Kinariwala has been at the forefront of delivering precise and reliable calibration, testing, and validation solutions across various industries. His expertise in providing services that meet international calibration standards has earned the trust of major clients, including Reliance Industries, Zydus Cadila, Indian Oil, ONGC, Adani, and Tata.
With a deep understanding of instrumentation, measurement accuracy, and industrial testing, Mr. Kinariwala ensures that each client receives exceptional service tailored to their specific needs. His unwavering commitment to quality and precision has established Prism Calibration as a trusted partner for some of the largest and most respected organizations in the industry.