Prism Calibration specializes in offering comprehensive calibration, audit, and consulting services. One of our key areas of expertise is conducting Hazard and Operability (HAZOP) studies. This article provides an in-depth guide on how to conduct a successful HAZOP study to enhance safety and minimize risks.
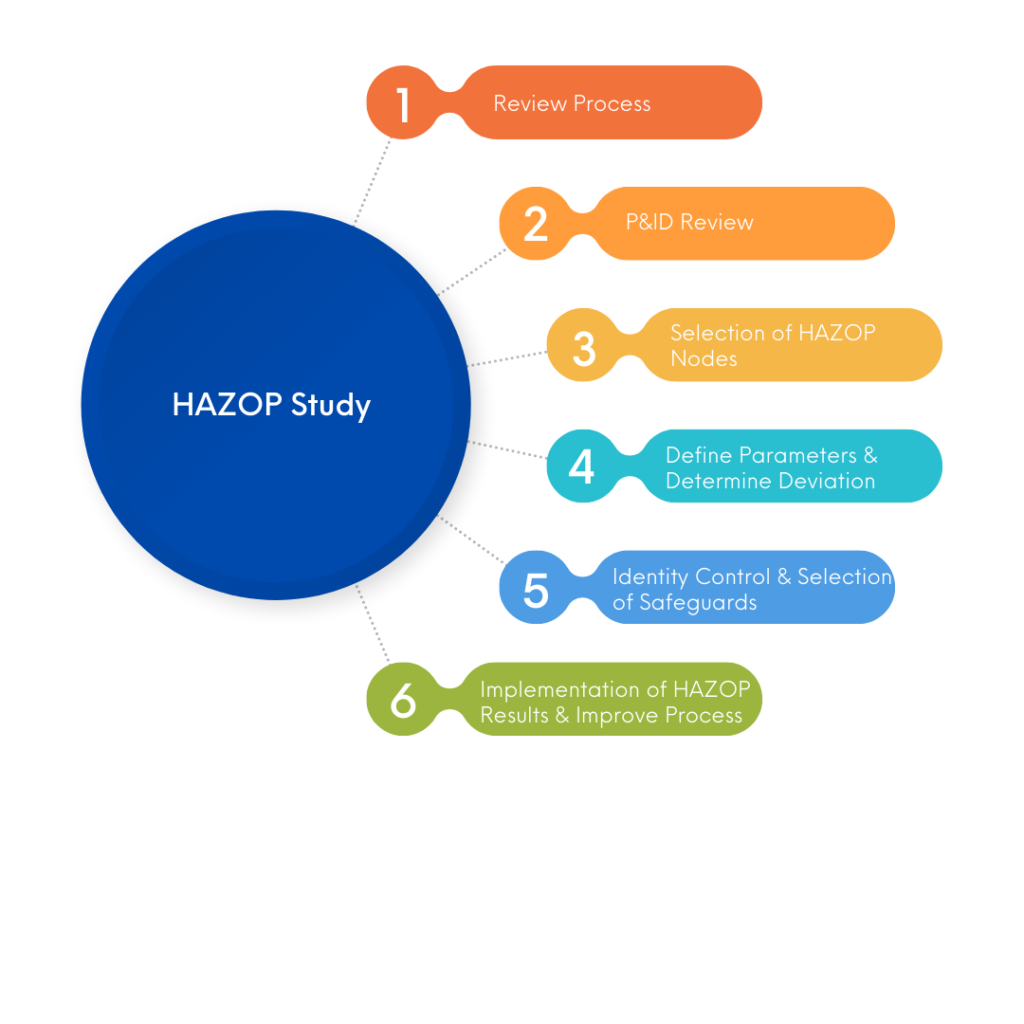
Introduction: Why HAZOP Studies Matter
Hazard and Operability Studies (HAZOPs) are a cornerstone of risk management and safety optimization in industrial processes. They systematically identify potential hazards, deviations, and operability issues to ensure the safety and efficiency of complex systems. Whether you’re working in chemical processing, manufacturing, or oil and gas, a well-conducted HAZOP study can save lives, reduce costs, and ensure compliance with regulatory standards.
1. Assemble a Multidisciplinary Team
A successful HAZOP study begins with forming a diverse team of experts, including:
- Process engineers: Provide technical insights.
- Safety professionals: Assess potential risks.
- Operators and maintenance staff: Offer practical knowledge of the system.
- Managers or decision-makers: Ensure alignment with organizational objectives.
The team’s combined expertise ensures a comprehensive analysis.
2. Define the Scope and Objectives
Clearly outline the study’s purpose and the specific system or process under review. Key steps include:
- Identifying boundaries of the process.
- Gathering relevant data, such as process flow diagrams (PFDs), piping and instrumentation diagrams (P&IDs), and operational procedures.
- Setting clear goals, such as identifying risks or improving operability.
3. Identify Critical Process Parameters
Process parameters are the variables that define system performance. Examples include:
- Temperature and pressure: Crucial for chemical and thermal processes.
- Flow rates and chemical composition: Impact operational efficiency and safety.
- Equipment-specific metrics: Such as pump capacity or tank levels.
These parameters form the foundation for identifying deviations.
4. Node Identification: Divide and Conquer
Break the process into smaller sections or “nodes” for focused analysis. Each node represents a distinct part of the system, such as:
- A pump and its associated piping.
- A reactor vessel and its controls.
This segmentation ensures no part of the process is overlooked.
5. Identify Deviations
Using guide words like “no,” “less,” “more,” “reverse,” or “as well as,” systematically analyze each node to uncover deviations from the design intent. Common examples include:
- No flow: Indicating a blockage or pump failure.
- High temperature: Suggesting equipment malfunction or improper control.
6. Conduct Risk Assessments
Evaluate the likelihood, severity, and consequences of each deviation. Use tools like risk matrices or Failure Mode and Effects Analysis (FMEA) to prioritize risks. Key considerations include:
- Impact on safety and health.
- Environmental consequences.
- Economic losses due to downtime or damage.
7. Recommend Mitigation Measures
For each identified risk, propose actionable solutions, such as:
- Process redesigns or equipment upgrades.
- Enhanced monitoring systems.
- Updated safety protocols or operator training.
8. Documentation: Capture the Insights
Thorough documentation ensures transparency and compliance. A comprehensive HAZOP report should include:
- A summary of deviations and risks.
- Proposed mitigation measures.
- Graphical representations, like annotated P&IDs.
9. Review and Approval
Present findings to stakeholders, including management and relevant departments. Their feedback is critical for refining recommendations and ensuring alignment with business goals.
10. Implementation of Mitigation Measures
Turn insights into action by implementing recommended changes. Ensure modifications adhere to safety and regulatory standards.
11. Monitoring and Continuous Review
Once changes are implemented:
- Regularly monitor the system for new risks.
- Schedule periodic HAZOP reviews, especially after significant process changes or incidents.
12. Training and Awareness
Conduct training programs to educate employees on:
- Identified risks and mitigation strategies.
- Updated operational and safety procedures.
Empowering personnel reduces human error and fosters a safety-first culture.
Why Choose Prism Calibration for Your HAZOP Study?
At Prism Calibration, we bring unmatched expertise in conducting HAZOP studies. Our systematic approach ensures that every potential hazard is identified and mitigated. With years of experience in calibration, audits, and consulting, we provide practical and compliant solutions tailored to your industry.
Frequently Asked Questions
What is the HAZOP methodology?
HAZOP, or a Hazard and Operability Study, is a systematic way to identify possible hazards in a work process. In this approach, the process is broken down into steps, and every variation in work parameters is considered for each step, to see what could go wrong.
What is HAZOP preparation phase?
HAZOP preparation phase
Start-up meeting to agree on the battery limits and intention with the HAZOP. In the start-up meeting, the participant list, agenda, and venue for the HAZOP should be agreed upon. It is important that the number of days for the HAZOP is set according to the scope of the HAZOP.
What is HAZOP checklist?
Hazard and Operability Analysis (HAZOP) is a structured and systematic technique for. system examination and risk management. In particular, HAZOP is often used as a. technique for identifying potential hazards in a system and identifying operability problems. likely to lead to nonconforming products.
How many types of HAZOP are there?
The four types of HAZOP studies that are conducted are: process HAZOP, procedure HAZOP, human HAZOP and software HAZOP.
What is the main objective of HAZOP study?
The objective of the Traditional HAZOP study is (with collaboration of a multidisciplinary team of employees of contractors) to identify potential hazards operability issues in process (Hazard and Operability Analysis) and to propose preventing actions.