In the realm of industrial instrumentation, precise pressure measurement is the bedrock of efficient, safe, and high-quality processes. HART (Highway Addressable Remote Transducer) pressure transmitters are indispensable tools, offering both analog and digital communication for enhanced control and diagnostics. However, like any precision instrument, regular and accurate calibration is paramount to guarantee their reliability.
This informative guide will walk you through the essential aspects of calibrating a HART pressure transmitter, providing you with the knowledge for this vital task.
The fundamental need for HART pressure transmitter calibration
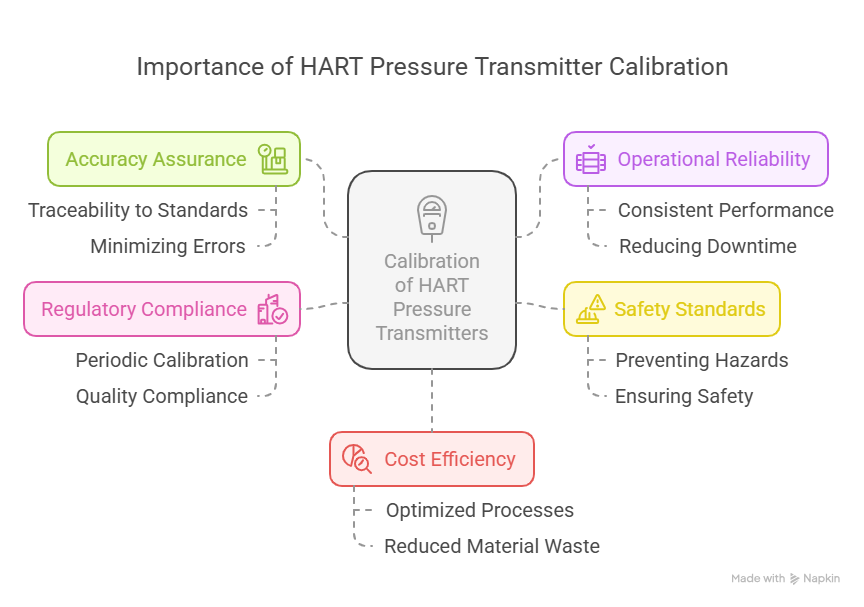
The reasons for diligently calibrating your HART pressure transmitter are manifold and directly impact your operational success:
- Accuracy assurance: Calibration establishes the traceability of your measurements to recognized standards, minimizing errors and ensuring the readings you rely on are precise.
- Maintaining operational reliability: Properly calibrated transmitters deliver consistent and dependable performance, reducing the likelihood of process disruptions and unexpected downtime.
- Upholding safety standards: In many industrial applications, accurate pressure readings are critical for preventing hazardous situations and ensuring the safety of personnel and equipment.
- Meeting regulatory requirements: Numerous industries are governed by regulations that mandate periodic instrument calibration to maintain product quality and safety compliance.
- Optimizing cost efficiency: Accurate measurements lead to optimized processes, reduced material waste, and the prevention of costly errors stemming from inaccurate data.
Key aspects of HART pressure transmitter calibration
Let’s delve into the key elements you need to understand for effective calibration:
1. Preparation: setting the stage for accurate calibration

Before you begin the calibration process, meticulous preparation is essential:
- Gathering the right tools: Ensure you have calibrated pressure standards (e.g., deadweight testers, pressure calibrators), a HART communicator (handheld or software-based for digital interaction), appropriate connecting hardware, and necessary safety equipment. The use of traceable and highly accurate standards is crucial.
- Consulting manufacturer documentation: Always refer to the specific calibration procedure outlined in the HART pressure transmitter’s datasheet and manual. This provides crucial model-specific guidance.
- Safe isolation: Prioritize safety by completely isolating the transmitter from the process and ensuring the system is fully depressurized before making any connections.
- Cleanliness is key: Ensure all connections are clean and free from any contaminants that could impede accurate pressure transmission.
2. Utilizing the power of the HART protocol for calibration
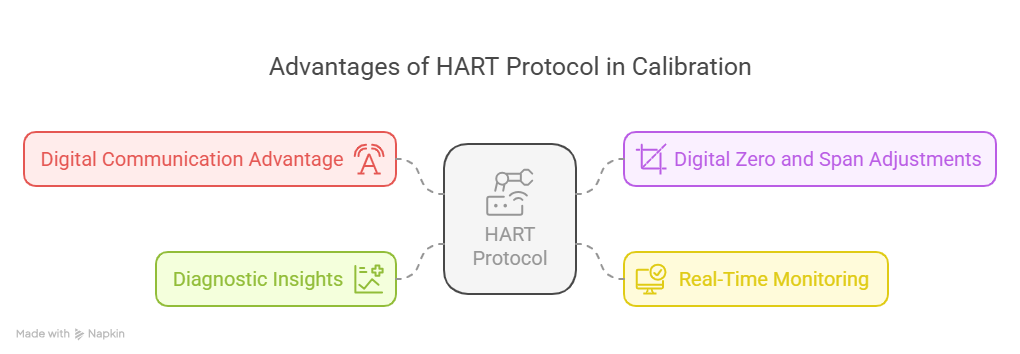
The HART protocol offers significant advantages during calibration:
- Digital communication advantage: The HART communicator allows direct digital communication with the transmitter, enabling you to read precise digital values alongside the analog output. This facilitates more accurate adjustments.
- Digital zero and span adjustments: Leverage the digital trim functions within the HART communicator to make precise adjustments to the transmitter’s zero and span points.
- Real-time monitoring: The HART communicator displays the applied pressure from your standard and the transmitter’s corresponding output simultaneously, allowing for immediate verification of adjustments.
- Diagnostic insights: The HART protocol also provides access to diagnostic information about the transmitter’s health, which can be valuable before and after calibration.
3. The Step-by-step calibration procedure
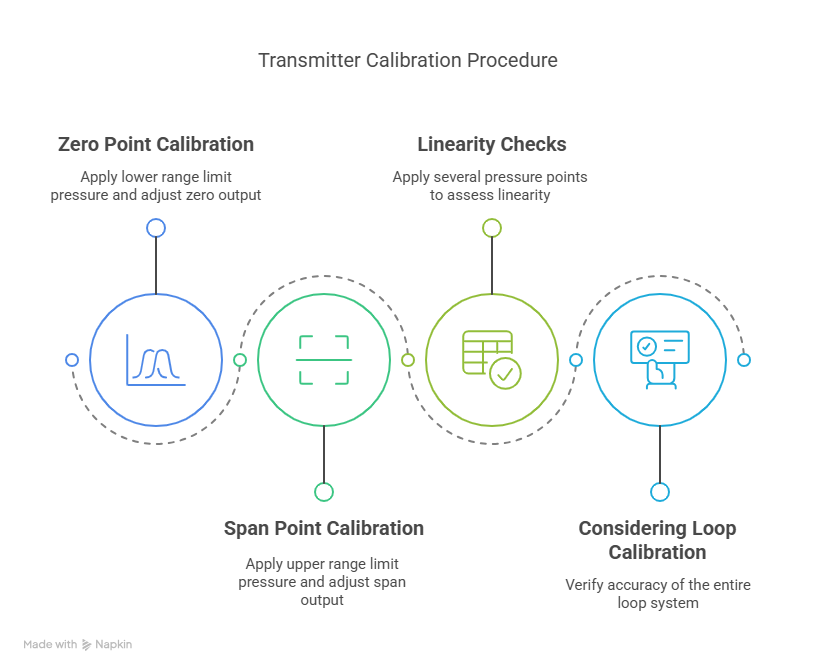
A systematic approach to calibration is crucial:
- Zero point calibration: Apply the lower range limit (LRL) pressure to the transmitter. Using the HART communicator, adjust the zero output to the expected value (e.g., 4 mA for a 4-20 mA loop). Verify this reading against your calibrated pressure standard.
- Span point calibration: Apply the upper range limit (URL) pressure to the transmitter. Using the HART communicator, adjust the span output to accurately reflect the applied pressure (e.g., 20 mA for a 4-20 mA loop). Again, verify against your standard.
- Linearity checks (Recommended): For a more thorough calibration, apply several pressure points across the transmitter’s range (e.g., 25%, 50%, 75% of the span). Record the input and output at each point to assess the transmitter’s linearity.
- Considering loop calibration: If the transmitter is part of a 4-20 mA loop, verifying the accuracy of the entire loop, including the receiving device, is essential for overall system accuracy.
4. Documentation
Thorough documentation is vital for traceability and quality assurance:
- Detailed record keeping: Meticulously record all aspects of the calibration process, including dates, instrument details, standards used (with their calibration information), as-found and as-left readings, adjustments made, and the technician’s information.
- Issuing calibration certificates: A formal calibration certificate provides documented evidence of the calibration performed and confirms traceability to recognized standards.
5. Maintaining accuracy over time:
Calibration is not a one-time event; ongoing maintenance is key:
- Establishing a calibration schedule: Implement a regular calibration interval based on manufacturer recommendations, application criticality, and historical data.
- Environmental awareness: Be mindful of environmental factors like temperature and humidity, which can impact accuracy.
- Regular checks: Consider performing periodic functional checks between formal calibration cycles.
Conclusion
Accurately calibrating your HART pressure transmitter is a fundamental practice for ensuring the reliability and accuracy of your industrial processes. By understanding the key aspects of preparation, utilizing the HART protocol effectively, following a systematic calibration procedure, and maintaining thorough documentation, you can significantly enhance the performance of your instruments.
How often should I calibrate my HART pressure transmitter? The calibration interval depends on several factors, including the manufacturer’s recommendations, the criticality of the application, environmental conditions, and your historical calibration data. A common starting point is every 6 to 12 months, but this can vary.
Frequently asked question
A HART communicator is a handheld device or software tool that allows you to communicate digitally with a HART pressure transmitter. It’s essential for accessing the transmitter’s configuration parameters, performing digital zero and span adjustments, and viewing diagnostic information, leading to more accurate calibration.
Calibration standards are highly accurate pressure sources with known traceability to national or international standards. They are used as the reference to which you compare and adjust the output of the HART pressure transmitter during calibration. Using traceable standards ensures the accuracy of your measurements.
Zero calibration involves adjusting the transmitter’s output to the correct value when the lower range limit (LRL) pressure is applied. Span calibration involves adjusting the output when the upper range limit (URL) pressure is applied. Both are crucial for ensuring accuracy across the entire operating range.
A linearity check involves applying several pressure points between the LRL and URL and verifying that the transmitter’s output is linear and accurate across this range. This helps identify any non-linearities in the transmitter’s performance.
Yes, field calibration is possible, but it’s important to ensure you have stable pressure sources and a controlled environment as much as possible. Bench calibration in a controlled workshop generally offers higher accuracy.
A calibration certificate should include details such as the date of calibration, the instrument’s identification, the standards used (with their calibration dates), as-found and as-left readings, any adjustments made, the environmental conditions during calibration, and the technician’s information.
Author bio
Mr. Parthiv Kinariwala is a leading expert in calibration and testing services, with over 20 years of experience in the industry. As the founder of Prism Calibration, established in 2004, Mr. Kinariwala has been at the forefront of delivering precise and reliable calibration, testing, and validation solutions across various industries. His expertise in providing services that meet international calibration standards has earned the trust of major clients, including Reliance Industries, Zydus Cadila, Indian Oil, ONGC, Adani, and Tata.
With a deep understanding of instrumentation, measurement accuracy, and industrial testing, Mr. Kinariwala ensures that each client receives exceptional service tailored to their specific needs. His unwavering commitment to quality and precision has established Prism Calibration as a trusted partner for some of the largest and most respected organizations in the industry.