In today’s fast-paced industrial environment, precision and accuracy are critical for ensuring efficient production processes and maintaining product quality. One technology that plays a crucial role in facilitating communication between field instruments and control systems is the Highway Addressable Remote Transducer (HART) protocol.Â
HART devices Calibrations are widely used in industries such as manufacturing, oil and gas, chemicals, and pharmaceuticals, where accuracy and reliability are paramount. However, to ensure that these devices continue to function optimally, regular calibration is essential.Â
This blog explores the importance of HART devices and why calibration is key to their performance in modern industries.
What are HART devices?
HART devices use the HART communication protocol to facilitate data transmission between sensors and control systems. This hybrid protocol enables digital signals to be transmitted over existing analog wiring, providing enhanced diagnostics, configuration, and real-time data without requiring new infrastructure.
- Hybrid communication: Transmits both analog and digital signals over the same wiring.
- Bidirectional communication: Allows for both data transmission and remote configuration or diagnostics.
- Real-time data: Provides continuous, real-time monitoring of important process parameters like temperature, pressure, flow, and level.
- Easy integration: Works with existing infrastructure, eliminating the need for new wiring or equipment.
Regular calibration is essential to ensure that HART devices perform accurately and consistently, helping industries avoid these risks and maintain optimal operation.
The benefits of regular calibration for HART devices
Maintaining a consistent calibration schedule for HART devices yields several key benefits:
- Improved efficiency: Accurate data leads to better control over production processes, which improves efficiency and reduces waste.
- Enhanced safety: Well-calibrated devices provide reliable measurements, which are critical in ensuring safe operating conditions in hazardous industries like oil and gas.
- Prolonged device lifespan: Regular calibration can extend the lifespan of HART devices by identifying issues before they lead to significant problems.
- Compliance with standards: Industries are often required to calibrate instruments regularly to meet safety and quality standards, ensuring compliance with local and international regulations.
- Cost savings: Accurate devices help avoid costly production errors, equipment failures, and unplanned downtime.
Why calibration of HART devices is crucial in industry
Over time, even the most precise instruments experience drift in their measurements. This can be caused by a variety of factors, including environmental conditions, regular wear and tear, and even subtle shifts in the materials of the device itself. Calibration is the process of adjusting these devices back to a reference standard to ensure they continue providing accurate data.
Without regular calibration, HART devices can produce inaccurate readings that can lead to:
- Operational inefficiencies: Incorrect measurements can result in suboptimal performance and wasted resources.
- Compromised product quality: In industries where precision is key, such as pharmaceuticals and food production, inaccurate data can lead to quality issues.
- Increased costs: Miscalibrated devices can cause production errors, leading to costly downtime or the need for rework.
- Safety risks: In environments like oil refineries or chemical plants, inaccurate data can pose significant safety hazards.
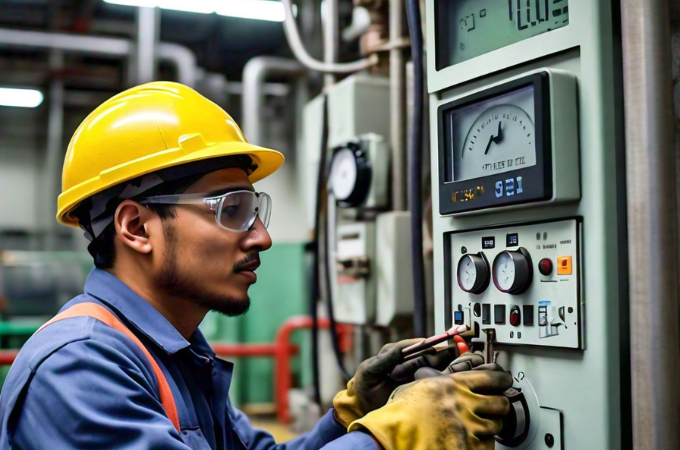
The importance of accurate data in industry
Data accuracy is the foundation of modern industrial processes. The following key areas depend heavily on precise and reliable data from HART devices:
- Process optimization: Accurate data enables companies to fine-tune processes, ensuring that they run at peak efficiency. For instance, in a manufacturing plant, accurate temperature and pressure readings help maintain optimal conditions for production.
- Cost control: Inaccurate measurements can lead to excessive energy consumption or material waste, driving up costs. Regular calibration ensures that devices provide the correct data, which allows for cost-effective operations.
- Regulatory compliance: Many industries are subject to strict regulations that require periodic calibration of measurement devices. Non-compliance can result in fines, production delays, or worse, legal penalties.
- Preventive maintenance: HART devices with accurate calibration help detect potential equipment failures before they happen. For example, a device may indicate an abnormal rise in pressure, signaling a potential system issue that can be addressed before it leads to equipment damage or downtime.
The calibration process: ensuring device accuracy and longevity
Calibrating HART devices involves comparing the device’s readings to a known reference standard, identifying any deviations, and adjusting the device to bring it back within the acceptable accuracy range. Here’s a more detailed look at the calibration process:
- Initial device inspection: Before calibration, a visual inspection of the HART device is essential. This helps identify any visible issues such as physical damage, corrosion, or signs of wear that may affect the device’s performance.
- Reference standard setup: A high-accuracy reference standard, traceable to national or international measurement standards, is required for calibration. This ensures that the calibration process is based on a known, precise measurement.
- Calibration procedure: The calibration procedure varies depending on the type of HART device being calibrated. The device’s output is compared with the reference : standard at various points across its operating range. If discrepancies are found, adjustments are made to bring the device’s readings in line with the standard.
- Documentation of results: Once the calibration is complete, the results are documented for record-keeping purposes. This includes recording the device’s pre-calibration and post-calibration accuracy. This documentation is often required for regulatory compliance and provides a history of the device’s performance over time.
- Recalibration scheduling: Calibration is not a one-time event. Devices must be recalibrated at regular intervals based on the manufacturer’s recommendations or industry best practices. Regular recalibration helps ensure long-term accuracy and reliability.
Challenges faced in calibrating HART devices
While calibration is essential, it comes with its own set of challenges. Some of the common issues include:
- Environmental conditions: Harsh industrial environments can affect the accuracy of HART devices, necessitating more frequent calibration.
- Complex systems: In large-scale industrial operations, the sheer number of devices can make it challenging to manage and schedule calibration for all equipment.
- Downtime for calibration: Calibration often requires taking devices offline, which can impact production if not properly planned. However, this can be mitigated by scheduling calibrations during planned maintenance windows.
Prism Calibration: your trusted partner for precision
At Prism Calibration, we understand the complexities and demands of modern industries. Our expert calibration services for HART devices ensure that your instruments deliver reliable and precise measurements, helping you maintain operational excellence.
With years of experience and state-of-the-art equipment, we offer calibration services tailored to your industry’s specific needs. From initial inspections to final adjustments, we ensure your devices remain accurate and compliant with industry standards.
Conclusion
The role of HART devices in modern industry is indispensable. These devices provide critical data that drive decision-making, process optimization, and safety in industries around the world. However, without regular calibration, the accuracy of this data can be compromised, leading to operational inefficiencies, increased costs, and safety risks.
At Prism Calibration, we are dedicated to helping industries maintain precision and reliability through our expert calibration services. By ensuring that your HART devices are regularly calibrated and functioning at peak performance, we help you avoid costly errors and ensure your business runs smoothly.
For expert calibration services that you can trust, look no further than Prism Calibration Contact Today.
Author Bio
Mr. Parthiv Kinariwala is a leading expert in calibration and testing services, with over 20 years of experience in the industry. As the founder of Prism Calibration, established in 2004, Mr. Kinariwala has been at the forefront of delivering precise and reliable calibration, testing, and validation solutions across various industries. His expertise in providing services that meet international calibration standards has earned the trust of major clients, including Reliance Industries, Zydus Cadila, Indian Oil, ONGC, Adani, and Tata.
With a deep understanding of instrumentation, measurement accuracy, and industrial testing, Mr. Kinariwala ensures that each client receives exceptional service tailored to their specific needs. His unwavering commitment to quality and precision has established Prism Calibration as a trusted partner for some of the largest and most respected organizations in the industry.