In the competitive industrial landscape, maximizing production efficiency is essential for success. One often-overlooked factor that significantly contributes to seamless operations is process instrument calibration. Regular calibration ensures that measurement tools used in the manufacturing process are functioning optimally, reducing errors and preventing unexpected production halts. This delves into how frequent calibration not only enhances precision but also plays a vital role in reducing production downtime, ultimately saving businesses time, money, and resources.
Why Process Instrument Calibration is Critical
Process instruments—such as thermometers, pressure gauges, flow meters, and level sensors—are vital in monitoring and controlling manufacturing processes across various industries, including oil and gas, pharmaceuticals, food and beverage, and chemicals. These instruments are responsible for collecting data that ensures equipment operates within designated safety and quality parameters.
Over time, even the most sophisticated instruments drift from their set parameters, often due to factors like environmental conditions, mechanical wear, or age. This drift, though gradual, can lead to inaccurate measurements that significantly impact production quality, safety, and efficiency. Without regular calibration, these inaccuracies can cause:
- Product defects, leading to rework or recalls
- Reduced process efficiency
- Violations of regulatory and quality standards
- Safety hazards for workers and equipment
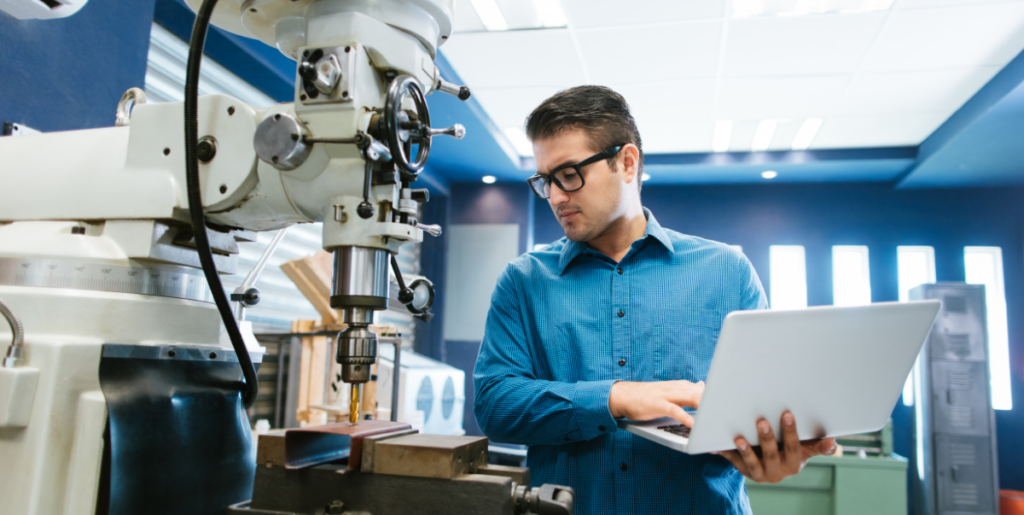
The role of calibration in minimizing downtime
Downtime is one of the most costly issues a business can face, and many factors contribute to it, including equipment failures, human errors, and poor instrument performance. Regular process instrument calibration addresses one of the most controllable causes—instrument inaccuracies—by ensuring that devices are delivering precise measurements and enabling smooth, uninterrupted production.
Here’s how regular calibration can help reduce production downtime:
Identifies potential failures before they occur
- Inaccurate instruments may not immediately lead to equipment failure but can cause errors that strain machinery over time.
- Regular calibration detects inaccuracies early, allowing for preventative maintenance, preventing severe equipment damage or costly unplanned downtime.
Enhances product quality and reduces waste
- Small deviations in measurement, especially in industries like pharmaceuticals or food processing, can cause significant product quality issues.
- Regular calibration ensures pressure, temperature, and chemical measurements are accurate, leading to consistent product quality and reducing stoppages due to rework or defective batches.
Maintains compliance with industry standards
- Many industries have strict regulations (ISO, FDA, GMP) that demand accurate instrumentation.
- Regular calibration ensures compliance, avoiding fines, legal issues, or forced production shutdowns due to non-compliance.
Optimizes process efficiency
- Accurate instruments provide reliable data in real time, which helps optimize production parameters such as speed, temperature, and pressure.
- This reduces unnecessary machine adjustments or stoppages, ensuring smooth operations and minimizing unplanned downtime.
Extends equipment lifespan
- Regularly calibrated instruments work in harmony with other equipment, preventing machinery from operating outside its intended range.
- This timely detection of wear or errors extends the life of machines, reducing the need for costly repairs or replacements.
Increases safety
- Instruments that provide accurate data help maintain operational safety, especially in industries dealing with hazardous materials or complex processes.
- Regular calibration minimizes the risk of accidents, ensuring safe working environments.
Reduces operational costs
- By avoiding downtime, improving product quality, and extending equipment life, calibration reduces overall operational costs.
- Fewer errors lead to lower expenses related to waste, repairs, and regulatory fines.
The calibration process: A detailed breakdown
Understanding the steps involved in calibration helps highlight how this process contributes to minimizing production downtime. Below are the key stages of calibration:
- Initial evaluation: The instrument is inspected for visible signs of wear, damage, or contamination. The technician records the instrument’s current performance and compares it to the expected performance standards.
- Reference standard comparison: The instrument is tested against a calibrated reference standard that is traceable to national or international standards. This ensures that the measurements align with global accuracy benchmarks.
- Adjustment and repair: If the instrument is found to be outside its tolerance range, adjustments are made to bring it back to its original specifications. This might include repairs, fine-tuning, or part replacement.
- Verification of results: Once adjustments are made, the instrument is re-tested to ensure it is working accurately within its prescribed limits.
- Documentation and certification: Calibration results are documented, and a calibration certificate is issued. This certificate can be used for regulatory audits and compliance purposes, showing that the equipment meets industry standards.
- Recalibration scheduling: Instruments are placed on a recalibration schedule, ensuring that the calibration is revisited at regular intervals, thus maintaining ongoing accuracy and minimizing the risk of drift.
Benefits of partnering with a professional calibration service
- Expertise and precision: Professional calibration services,offer highly specialized equipment and expert technicians for calibration to the highest standards.
- Certified standards: Certified reference materials and compliance with international standards ensure top-tier accuracy and regulatory compliance.
- Minimized risk: Outsourcing to a professional service reduces the risk of errors, enhances reliability, and minimizes production downtime.
Conclusion
Regular process instrument calibration is essential for maintaining operational efficiency, improving product quality, and minimizing production downtime. Investing in calibration services ensures compliance with industry standards, optimizes process performance, and extends the lifespan of your equipment. At Prism Calibration, we provide expert calibration solutions tailored to meet your industry needs.
For professional calibration services, contact us today to learn how we can help you keep your operations running smoothly and efficiently.
FAQs
The frequency of calibration depends on the type of instrument, its usage, and industry regulations. Typically, instruments are calibrated annually, but high-precision environments may require more frequent checks.
While in-house calibration is possible, it often requires specialized equipment and expertise. Partnering with a professional service ensures higher accuracy and traceable results, especially for complex instruments.
Industries like pharmaceuticals, food and beverage, oil and gas, chemical manufacturing, and aerospace rely heavily on precise measurements and therefore benefit greatly from routine calibration
Uncalibrated instruments can lead to inaccurate measurements, reduced product quality, non-compliance with regulations, and unexpected production downtime due to equipment failure.
Regular calibration ensures instruments provide accurate data, allowing machinery to operate within safe parameters, reducing the risk of accidents or hazardous incidents in the workplace.
Frequent product inconsistencies, equipment malfunctions, or deviations in process control may indicate that instruments need recalibration.
Yes, outsourcing calibration to professionals minimizes errors, ensures regulatory compliance, and reduces downtime, ultimately saving costs in the long run.
Author Bio
Mr. Parthiv Kinariwala is a leading expert in calibration and testing services, with over 20 years of experience in the industry. As the founder of Prism Calibration, established in 2004, Mr. Kinariwala has been at the forefront of delivering precise and reliable calibration, testing, and validation solutions across various industries. His expertise in providing services that meet international calibration standards has earned the trust of major clients, including Reliance Industries, Zydus Cadila, Indian Oil, ONGC, Adani, and Tata.
With a deep understanding of instrumentation, measurement accuracy, and industrial testing, Mr. Kinariwala ensures that each client receives exceptional service tailored to their specific needs. His unwavering commitment to quality and precision has established Prism Calibration as a trusted partner for some of the largest and most respected organizations in the industry.