In industries such as oil and gas, manufacturing, Safety and utilities, accurate instrumentation is paramount to ensure safety, compliance, and operational efficiency. HART (Highway Addressable Remote Transducer) devices, widely used for their ability to provide digital communication alongside the standard 4-20mA analog signal, play a vital role in process automation.
Regular calibration of these devices is essential not only for maintaining efficiency but also for ensuring safety across operations. why regular calibration of HART devices is crucial for both safety and efficiency and how neglecting this process can lead to costly and dangerous consequences.
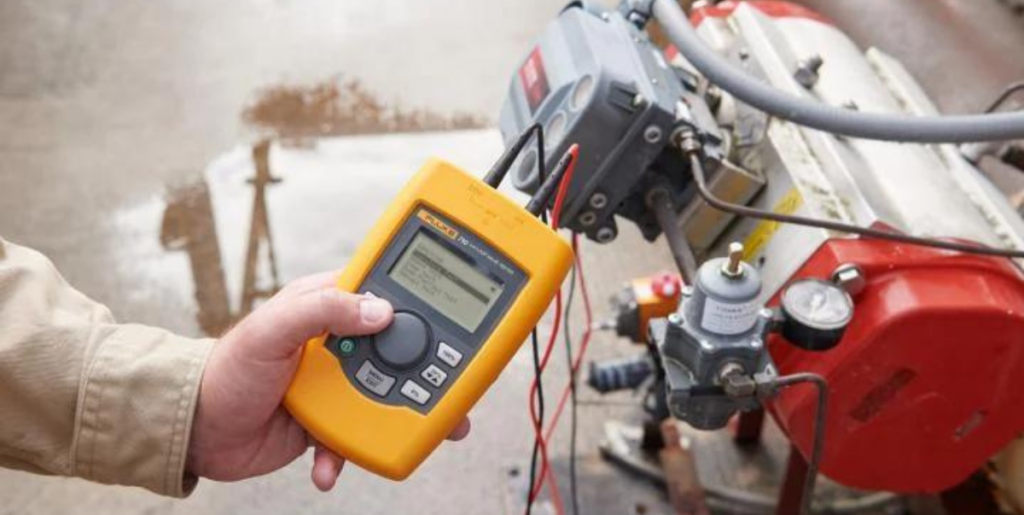
What is calibration and why is it important?
- Ensures accurate measurements: Calibration adjusts and verifies a device’s performance against known standards to ensure that it provides correct and reliable readings.
- Prevents instrument drift: Over time, instruments like HART devices can “drift,” meaning their readings become less accurate due to factors like wear, environmental conditions, or signal degradation.
- Maintains compliance with standards: Many industries are regulated by standards such as ISO 9001, IEC 61511, or OSHA, which require regular calibration to ensure compliance and operational safety.
- Reduces risk of system failures: Uncalibrated devices can lead to incorrect data, which may trigger malfunctions, equipment breakdowns, or even catastrophic system failures.
- Supports regulatory audits: Regular calibration ensures your equipment meets industry regulations and is audit-ready, helping to avoid penalties, fines, or legal complications.
- Improves process control: By calibrating devices, businesses can ensure better control over their processes, resulting in higher precision, reduced waste, and improved overall quality of output.
- Enhances decision-making: Accurate data provided by well-calibrated devices allows operators to make informed decisions, optimizing workflow and resource allocation.
The role of HART devices in industrial processes
- Real-time process monitoring: HART devices are commonly used to measure and control essential parameters such as pressure, temperature, flow, and levels in complex industrial environments.
- Critical data collection: These devices gather and communicate critical data, providing real-time insights that ensure processes are running as expected.
- Diagnostics & communication: The digital communication features of HART technology enable advanced diagnostics, allowing operators to identify potential issues before they become critical.
- Safety automation: In high-risk industries like oil refineries or chemical plants, HART devices contribute to safety automation by triggering alarms or shutting down systems in hazardous conditions.
- Integration with control systems: HART devices are often integrated with SCADA (Supervisory Control and Data Acquisition) and DCS (Distributed Control Systems) to automate industrial processes, making accurate calibration even more essential.
Why regular calibration is crucial for safety
- Prevents equipment verload: If devices like pressure transducers or flow meters are not calibrated, they may provide faulty readings, leading to overloading of systems, causing equipment failures, explosions, or fires.
- Ensures safe environmental conditions: HART devices used for toxic gas detection or monitoring chemical levels must provide precise data to avoid hazardous exposure to workers and the environment.
- Reduces accident risks: Improper readings can result in dangerous operating conditions, such as excessive heat or pressure, which can lead to worker injuries or fatalities.
- Avoids safety regulation breaches: Many industries are bound by safety regulations requiring accurate data for monitoring. Calibration helps you avoid compliance breaches and maintain a safe working environment.
- Reliable emergency systems: Devices that control emergency shutdown systems must be regularly calibrated to ensure they function when needed, especially in critical situations.
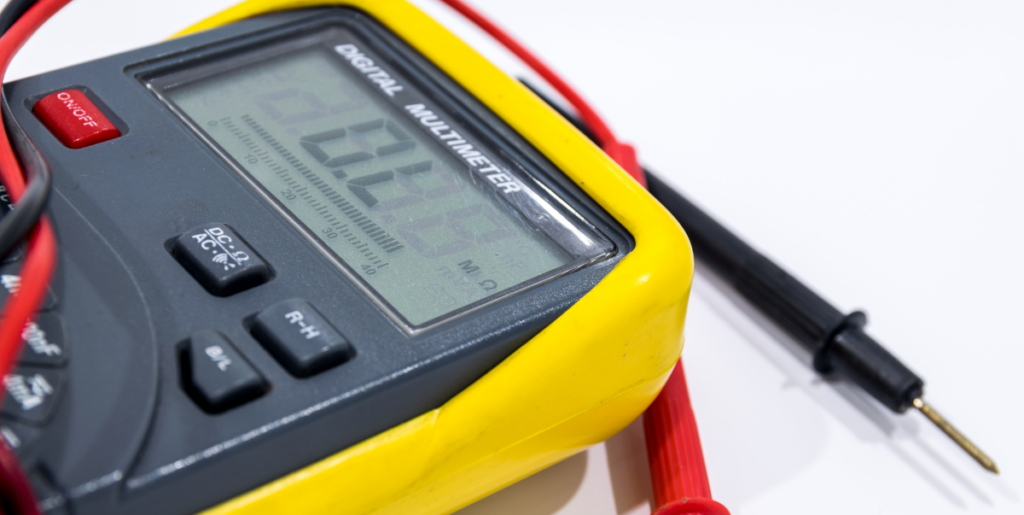
Why regular calibration is crucial for efficiency
- Improves production quality: Accurate measurements ensure that processes remain within specified tolerance levels, maintaining product quality and consistency.
- Optimizes resource utilization: Calibrated devices help minimize waste by ensuring efficient use of raw materials, energy, and time.
- Reduces unplanned downtime: By keeping devices calibrated, you reduce the likelihood of unexpected malfunctions that can result in costly downtime and production halts.
- Enhances equipment longevity: Regular calibration ensures that instruments operate within their designed specifications, which can extend the lifespan of both the devices and the equipment they control.
- Lowers operating costs: Misaligned or faulty instruments can lead to process inefficiencies and waste, increasing energy consumption and operational costs. Calibration ensures optimized performance, reducing these inefficiencies.
- Increases productivity: Consistently calibrated devices provide accurate data that allows operators to make quicker, better-informed decisions, which boosts overall productivity.
Risks of neglecting calibration
Failing to regularly calibrate HART devices can have significant consequences, including:
- Increased downtime: Unexpected equipment failures can lead to costly downtimes and production halts.
- Financial losses: Inaccurate readings can lead to inefficient operations, resulting in increased costs for raw materials, energy, and labor.
- Safety hazards: Misleading data from HART devices can pose serious safety risks to personnel and equipment.
Key Benefits of Regular HART Device Calibration
- Enhanced safety: Regular calibration prevents accidents, reduces risks, and ensures equipment operates under safe conditions.
- Compliance with regulations: It ensures that your systems meet all regulatory and safety standards, avoiding penalties or legal repercussions.
- Operational efficiency: Accurate measurements enable smoother processes, reduce inefficiencies, and enhance system performance.
- Lower maintenance costs: Prevents unplanned failures and reduces maintenance costs by keeping devices in top working condition.
- Optimized resource management: Regular calibration helps ensure minimal wastage of energy and materials, contributing to cost savings and environmental sustainability.
- Prolonged device lifespan: Well-maintained and calibrated devices last longer, reducing the need for frequent replacements.
- Data accuracy for decision-making: Provides reliable, high-quality data that helps operators make informed decisions, improving productivity and process control.
Calibration best practices
To ensure the proper functioning of HART devices, it is essential to follow some best practices for calibration:
- Create a regular calibration schedule: Follow the manufacturer’s recommended intervals for calibration or develop a custom schedule based on usage patterns and environmental conditions.
- Use qualified calibration professionals: Always use certified professionals or trusted third-party calibration service providers for accurate and traceable calibration.
- Utilize traceable calibration standards: Ensure that calibration is done using traceable standards, like those certified by national or international bodies such as NIST.
- Document calibration activities: Keep accurate records of calibration dates, results, and any corrective actions taken. These records can prove vital for audits and quality management systems.
- Consider calibration automation: For large-scale operations, automated calibration systems can be employed to ensure that all devices are calibrated on time without manual intervention.
- Review and update calibration procedures: Regularly review your calibration procedures to align with any updates in industry standards or technology advancements.
- Check calibration for critical devices more frequently: Devices that play a critical role in safety or process control should be calibrated more frequently than others.
Conclusion
Regular calibration of HART devices is a critical aspect of maintaining safety and efficiency in industrial operations. Failing to regularly calibrate these devices can lead to operational inefficiencies, regulatory non-compliance, and even catastrophic accidents. By ensuring that your HART devices are calibrated regularly and accurately, you can prevent safety hazards, reduce operational costs, and extend the life of your equipment.
For industries that rely on HART devices, partnering with a professional calibration service provider like Prism Calibration ensures that all devices remain accurate, compliant, and safe. With a proactive approach to calibration, you can keep your operations running smoothly while safeguarding both personnel and assets.
Contact us today for professional calibration services tailored to your industry needs!
FAQs
Calibration frequency depends on the device type, manufacturer recommendations, and operational conditions. Generally, annual calibration is advisable, but some industries may require more frequent checks.
Signs include inconsistent readings, frequent alarms, or discrepancies between actual process conditions and sensor output.
Miscalibrated devices can lead to safety hazards, operational inefficiencies, regulatory fines, and increased maintenance costs.
Look for providers with industry experience, certifications, and a solid reputation. They should also be familiar with your specific HART devices and regulatory requirements.
Author Bio
Mr. Parthiv Kinariwala is a leading expert in calibration and testing services, with over 20 years of experience in the industry. As the founder of Prism Calibration, established in 2004, Mr. Kinariwala has been at the forefront of delivering precise and reliable calibration, testing, and validation solutions across various industries. His expertise in providing services that meet international calibration standards has earned the trust of major clients, including Reliance Industries, Zydus Cadila, Indian Oil, ONGC, Adani, and Tata.
With a deep understanding of instrumentation, measurement accuracy, and industrial testing, Mr. Kinariwala ensures that each client receives exceptional service tailored to their specific needs. His unwavering commitment to quality and precision has established Prism Calibration as a trusted partner for some of the largest and most respected organizations in the industry.