In various industries such as healthcare, pharmaceuticals, and research laboratories, deep freezers play a crucial role in preserving samples and sensitive materials. However, to ensure the reliability and accuracy of these deep freezers, regular calibration is essential. This article explores the significance of regular deep freezer calibration in maintaining precision and compliance with industry standards.
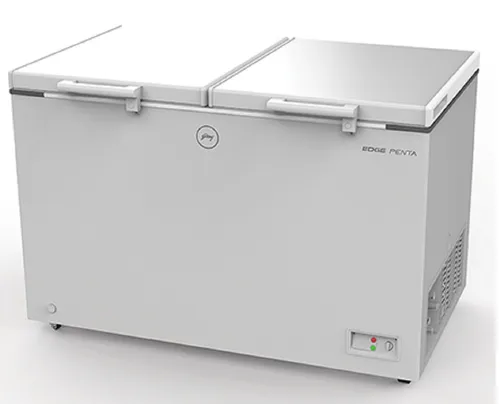
Understanding Deep Freezer Calibration
Deep freezer calibration involves the process of adjusting and verifying the accuracy of temperature settings to maintain optimal storage conditions for samples. It ensures that the freezer maintains the desired temperature consistently, preventing fluctuations that could compromise the integrity of stored materials.
Ensuring Precision through Calibration
Calibration helps in maintaining the precision of deep freezers by correcting any deviations from the set temperature. This precision is critical for preserving the quality of samples, especially in industries where accuracy is paramount, such as healthcare and research.
Compliance with Regulations
Regulatory bodies often mandate regular calibration of deep freezers to ensure compliance with industry standards and guidelines. Failure to comply with these regulations can result in legal consequences and jeopardize the reputation of the organization.
Frequency of Calibration
The frequency of deep freezer calibration depends on various factors, including the type of freezer, usage patterns, and industry regulations. However, it is generally recommended to calibrate deep freezers at least once a year or more frequently if they are subjected to heavy use.
Calibration Process
The calibration process involves a series of steps, including temperature measurement, adjustment of settings, and verification of accuracy using calibrated instruments. It requires specialized tools and trained personnel to ensure precise results.
Benefits of Regular Calibration
Regular calibration of deep freezers offers numerous benefits, including ensuring the reliability of stored samples, prolonging the lifespan of equipment, and minimizing the risk of temperature excursions that could lead to sample degradation.
Risks of Neglecting Calibration
Neglecting calibration can lead to inaccurate temperature readings, which may compromise the quality of stored samples and result in costly losses for the organization. Additionally, it can lead to non-compliance with regulatory requirements, resulting in fines and other penalties.
Selecting a Calibration Service
When choosing a calibration service provider, it is essential to consider factors such as accreditation, experience, and reputation in the industry. Working with a reputable service provider ensures accurate calibration results and compliance with regulatory standards.
Best Practices for Calibration
Maintaining detailed documentation of calibration activities and providing regular training to staff members responsible for deep freezer maintenance are essential best practices. These practices help ensure consistency and reliability in calibration procedures.
Common Calibration Challenges
Temperature fluctuations and equipment malfunctions are common challenges faced during the calibration process. However, proactive maintenance and troubleshooting can help mitigate these issues and ensure accurate calibration results.
Case Studies
Case studies highlighting successful calibration efforts and lessons learned from calibration failures provide valuable insights into the importance of regular deep freezer calibration and its impact on sample integrity.
Future Trends in Calibration
Advancements in calibration technology, such as automation and remote monitoring, are expected to streamline the calibration process and improve efficiency. These innovations offer opportunities for greater precision and accuracy in temperature control.
Conclusion
Regular deep freezer calibration is essential for maintaining precision and compliance with industry standards. By ensuring accurate temperature settings, calibration helps preserve the integrity of stored samples and minimizes the risk of non-compliance with regulatory requirements.
FAQs (Frequently Asked Questions)
How often should deep freezers be calibrated?
Deep freezers should be calibrated at least once a year, or more frequently if required by industry regulations or usage patterns.
Can I calibrate my deep freezer myself?
While it is possible to calibrate a deep freezer yourself, it is recommended to hire a professional calibration service provider for accurate and reliable results.
What are the consequences of skipping calibration?
Skipping calibration can lead to inaccurate temperature readings, compromising the quality of stored samples and risking non-compliance with regulatory requirements.
Is calibration necessary for all types of deep freezers?
Yes, calibration is necessary for all types of deep freezers to ensure accurate temperature control and preserve sample integrity.
What should I look for in a calibration service provider?
When selecting a calibration service provider, look for accreditation, experience, and a reputation for reliability and accuracy in calibration services.
Author Bio
Mr. Parthiv Kinariwala is a leading expert in calibration and testing services, with over 20 years of experience in the industry. As the founder of Prism Calibration, established in 2004, Mr. Kinariwala has been at the forefront of delivering precise and reliable calibration, testing, and validation solutions across various industries. His expertise in providing services that meet international calibration standards has earned the trust of major clients, including Reliance Industries, Zydus Cadila, Indian Oil, ONGC, Adani, and Tata.
With a deep understanding of instrumentation, measurement accuracy, and industrial testing, Mr. Kinariwala ensures that each client receives exceptional service tailored to their specific needs. His unwavering commitment to quality and precision has established Prism Calibration as a trusted partner for some of the largest and most respected organizations in the industry.