In industries such as pharmaceuticals, food production, and research laboratories, Environment the integrity of temperature-sensitive products is paramount. Deep freezers play a vital role in preserving these materials, but their effectiveness hinges on accurate temperature control. Regular calibration of deep freezers is essential for quality assurance. In this blog, we will delve into the importance of deep freezer calibration, the process involved, and how it contributes to maintaining product integrity and regulatory compliance.
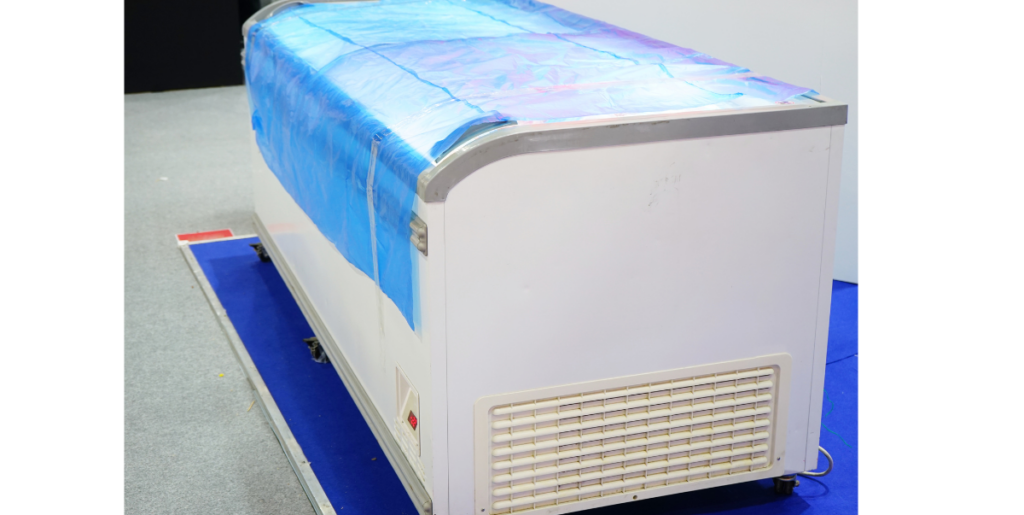
Understanding deep freezer calibration
Calibration is the process of adjusting an instrument to ensure that its measurements correspond to established standards. For deep freezers, this means verifying that the internal temperature settings align with actual measurements taken inside the unit. This process is crucial, especially for freezers that maintain extremely low temperatures, as even slight deviations can affect the quality and safety of stored products.
Why calibration matters
- Maintaining product integrity: Many products, particularly in the pharmaceutical and food industries, are sensitive to temperature variations. For example, vaccines must be stored at specific temperatures to maintain their efficacy. Regular calibration ensures that deep freezers provide the precise conditions required for product integrity.
- Regulatory compliance: Many industries operate under strict regulations regarding the storage of temperature-sensitive products. Organizations must comply with standards set by regulatory bodies, such as the FDA or EMA. Regular calibration of deep freezers is essential to demonstrate compliance, avoiding fines and legal repercussions.
- Preventing financial loss: Temperature fluctuations can lead to spoilage and waste. For instance, a pharmaceutical company may lose thousands of dollars in vaccine inventory if a freezer malfunctions. Investing in regular calibration minimizes the risk of such financial losses.
- Enhancing operational efficiency: Accurately calibrated deep freezers operate more efficiently, consuming less energy. When freezers maintain the correct temperature without fluctuations, they reduce energy costs and contribute to more sustainable operations.
- Building customer trust: In industries where product quality is critical, demonstrating a commitment to regular calibration can enhance customer trust. Clients want to know that their products are stored under optimal conditions, and proper calibration provides assurance of that.
Signs your deep freezer needs calibration
Recognizing when your deep freezer requires calibration is essential for maintaining quality assurance. Here are some signs to watch for:
- Inconsistent temperature readings: If the display shows a different temperature than what you expect based on internal conditions, it’s a clear indicator that calibration is needed.
- Frequent temperature alarms: If your freezer frequently triggers alarms, it may indicate that the temperature is fluctuating outside the desired range, suggesting a need for recalibration.
- Physical changes in stored products: Look for frost buildup, ice crystals on frozen items, or thawed products, as these signs may indicate temperature instability.
- Previous calibration history: If it has been a year or longer since the last calibration, it’s time to schedule a new one, regardless of any obvious issues.
The Calibration Process
- Preparation: Ensure that the deep freezer is clean and free from obstructions. Allow the unit to stabilize at the desired set point for at least 24 hours.
- Measurement: Use calibrated temperature sensors or thermocouples to measure the internal temperature at various points within the freezer. It’s advisable to take multiple readings at different locations to account for temperature variations within the unit.
- Adjustment: If discrepancies are found between the actual temperature and the set point, adjustments should be made according to the manufacturer’s specifications. Some models may require adjustments via control panels, while others may need manual recalibration.
- Documentation: Record all calibration results, including the date, personnel involved, initial and adjusted temperatures, and any actions taken. This documentation is essential for compliance and helps track performance over time.
- Follow-Up checks: Schedule follow-up checks to ensure that the adjustments made during calibration have held. This can help identify any ongoing issues with the unit.
Common challenges in deep freezer calibration
While calibration is essential, it can present several challenges:
- Temperature gradient: Deep freezers can have temperature variations within the unit, which can affect calibration accuracy. It’s important to measure temperatures at various points to account for these differences.
- Environmental factors: External factors such as humidity and air circulation can impact the performance of a deep freezer. Ensuring a stable environment is crucial for accurate calibration.
- Equipment drift: Over time, the performance of a deep freezer can drift from its original settings. Regular checks and calibrations are necessary to maintain accuracy.
Best practices for deep freezer calibration
- Establish a calibration schedule: Create a routine calibration schedule based on the specific requirements of your operations. This ensures that calibrations are not overlooked.
- Use qualified personnel: Ensure that only trained personnel carry out calibrations. This minimizes errors and ensures compliance with industry standards.
- Leverage technology: Utilize advanced calibration tools and software that can provide more accurate readings and streamline the documentation process.
- Regularly review performance: Monitor the performance of your deep freezers regularly. Use the collected data to identify trends and make informed decisions about maintenance and calibration needs.
- Document everything: Keep thorough records of all calibration activities, including results and adjustments. This documentation is crucial for audits and quality assurance.
Benefits of professional calibration services
While in-house calibration is possible, partnering with a professional calibration service offers significant advantages:
- Expertise: Professional technicians have the training and experience necessary to conduct accurate calibrations. They are familiar with industry standards and best practices.
- Advanced equipment: Calibration service providers utilize high-precision instruments that may not be available in-house, resulting in more reliable calibration results.
- Traceability: Professional services provide traceable calibration certificates, which are essential for audits and regulatory compliance. These certificates verify that the calibration meets national or international standards.
- Time savings: Outsourcing calibration allows your team to focus on core business activities while ensuring that all equipment remains compliant and functional.
Conclusion
Regular calibration of deep freezers is crucial for maintaining quality assurance in industries that depend on precise temperature control. By ensuring that deep freezers operate accurately, organizations can preserve product integrity, comply with regulations, prevent financial losses, and enhance operational efficiency. Investing in regular calibration and partnering with a professional service provider can safeguard your operations and ensure that your temperature-sensitive products remain safe and effective.
For tailored calibration services that meet your industry needs, contact Prism Calibration today!
FAQs
The frequency of calibration typically depends on the specific application, but it’s generally recommended to calibrate deep freezers at least once a year. For critical applications or environments with frequent use, more frequent calibrations may be necessary.
Signs include inconsistent temperature readings, frequent temperature alarms, visible frost buildup or ice crystals on products, and physical changes in the stored items. If it’s been over a year since the last calibration, it’s time to schedule one regardless of these signs.
While some organizations may have trained personnel, it is often advisable to hire a professional calibration service. Professionals have the expertise and tools to perform accurate calibrations that meet industry standards.
Failing to calibrate a deep freezer can result in inaccurate temperature readings, which can compromise product safety and quality. This can lead to spoilage, financial losses, and regulatory non-compliance, potentially resulting in legal issues.
When selecting a calibration service provider, consider their accreditation, experience in your specific industry, the quality of their equipment, and their ability to provide traceable calibration certificates. Reviews and testimonials can also help inform your decision.
Professional calibration services offer expertise, advanced equipment, traceable calibration certificates, and time savings. They ensure compliance with industry standards and help maintain the integrity of temperature-sensitive products.
To ensure efficient operation, establish a regular calibration schedule, use qualified personnel for calibration, monitor performance regularly, and document all calibration activities. This proactive approach helps maintain optimal performance.
Deep freezers are commonly used to store pharmaceuticals, vaccines, biological samples, frozen food, and other temperature-sensitive materials. Each of these products has specific temperature requirements that must be monitored and maintained.
Yes, environmental factors such as humidity, temperature fluctuations in the storage area, and air circulation can impact deep freezer performance. It is important to keep the freezer in a controlled environment to ensure accurate calibration and optimal operation.
Yes, calibration specifically refers to the process of adjusting and verifying the accuracy of measurement instruments. Maintenance involves general upkeep and repairs to ensure that equipment functions correctly over time, which may include cleaning, replacing worn parts, and checking seals.
Author Bio
Mr. Parthiv Kinariwala is a leading expert in calibration and testing services, with over 20 years of experience in the industry. As the founder of Prism Calibration, established in 2004, Mr. Kinariwala has been at the forefront of delivering precise and reliable calibration, testing, and validation solutions across various industries. His expertise in providing services that meet international calibration standards has earned the trust of major clients, including Reliance Industries, Zydus Cadila, Indian Oil, ONGC, Adani, and Tata.
With a deep understanding of instrumentation, measurement accuracy, and industrial testing, Mr. Kinariwala ensures that each client receives exceptional service tailored to their specific needs. His unwavering commitment to quality and precision has established Prism Calibration as a trusted partner for some of the largest and most respected organizations in the industry.